摘要:二氧化硫是當今陶瓷生產(chǎn)過程中產(chǎn)生的主要大氣污染物之一,而對陶瓷企業(yè)排放的廢氣進行治理是環(huán)境保護的重要課題。本文介紹了現(xiàn)階段陶瓷行業(yè)的脫硫技術(shù),從實用性角度闡述了幾種脫硫技術(shù)用于陶瓷企業(yè)廢氣脫硫的適應(yīng)性及優(yōu)缺點,以供陶瓷企業(yè)在選擇脫硫技術(shù)時進行參考。
前言
我國是世界陶瓷最大生產(chǎn)國,陶瓷產(chǎn)量占全球總產(chǎn)量約70%;同時也是主要的陶瓷出口國,年產(chǎn)量與出口額均居世界首位[1]。陶瓷工業(yè)在為我國經(jīng)濟建設(shè)做出重大貢獻的同時,也帶來嚴重的大氣污染問題。目前陶瓷工業(yè)已被列入國家環(huán)保規(guī)劃重點治理的行業(yè)之一。面對日益嚴峻的環(huán)保形勢,環(huán)保部制定并頒布實施了《陶瓷工業(yè)污染物排放標準》(GB 25464-2010),對粉塵、SO2、NOx 等排放實施嚴格限值,2014 年國家環(huán)保部又發(fā)布了《陶瓷工業(yè)污染物排放標準》(GB25464-2010)的修改單。排放標準更為嚴苛,修改主要內(nèi)容為噴霧干燥塔、陶瓷窯的顆粒物限值調(diào)整為30mg/m3、SO2 限值調(diào)整為50mg/m3、NOx限值調(diào)整為180mg/m3。陶瓷工業(yè)排放的硫化物、氮氧化物和煙塵是造成極端天氣的主要污染物。因此,陶瓷工業(yè)排放污染物高效脫除是當前國際能源環(huán)境領(lǐng)域的戰(zhàn)略性前沿課題之一,也是研究的熱點和難點。針對煙氣脫硫,目前陶瓷行業(yè)常見的脫硫技術(shù)有雙堿法濕法脫硫、石灰石-石膏法濕法脫硫、半干法脫硫。
1 鈣鈉雙堿法煙氣脫硫
雙堿法煙氣脫硫采用氫氧化鈣和碳酸鈉作為脫硫劑,反應(yīng)初利用碳酸鈉和煙氣中SO2 反應(yīng)生成物亞硫酸鈉溶于水,含亞硫酸鈉的脫硫循環(huán)水與投加的氫氧化鈣反應(yīng)可生成氫氧化鈉和亞硫酸鈣。通過沉淀分離可將難溶的亞硫酸鈣從循環(huán)水中清除,氫氧化鈉易溶于水可循環(huán)使用,脫硫過程只消耗氫氧化鈣。
1.1 反應(yīng)機理
1)脫硫
Na2CO3+SO2 → Na2SO3+CO2
2NaOH+SO2 → Na2SO3+H2O
Na2SO3+SO2+H2O → 2NaHSO3
2)再生
Ca(OH)2+Na2SO3 → 2NaOH+CaSO3
Ca(OH)2+2NaHSO3 → Na2SO3+CaSO3+2H2O
鈣鈉雙減法脫硫具有工藝簡單、初期投資省等優(yōu)點。據(jù)相關(guān)統(tǒng)計目前約有80% 以上的陶瓷企業(yè),均采用鈣鈉雙堿法進行煙氣脫硫。
1.2 此法在陶瓷企業(yè)運行過程中存的問題
1)根據(jù)實際運行情況看,當按設(shè)計量投入CaO(制備Ca(OH)2 溶液)后,脫硫效果差;當適當增加CaO 投入量時,脫硫塔內(nèi)、噴頭結(jié)垢、堵塞嚴重。為保證脫硫效率廠家均選擇多投入NaOH 溶液,少用或不用CaO 量(再生),實際為鈉堿法脫硫,致使運行成本高。
2)由于陶瓷窯爐煙氣中氧濃度較高( 通常在16% 左),會氧化脫硫液中部分Na2SO3 并生成Na2SO4,而Na2SO4 無法被鈣離子置換,多次循環(huán)后,導(dǎo)致脫硫再生液中SO42− 離子濃度過高,峰值濃度最高可達5000mg/L,使得企業(yè)廢水處理壓力巨大。
2 石灰石- 石膏法煙氣脫硫
石灰石- 石膏法的整個反應(yīng)大致可以分為吸收和氧化兩個過程,先將石灰石粉加水制成漿液作為吸收劑泵入吸收塔與煙氣充分接觸混合,吸收二氧化硫,生成亞硫酸鈣,然后再與從塔下部鼓入的空氣進行氧化反應(yīng)生成硫酸鈣,硫酸鈣達到一定飽和度后,結(jié)晶形成石膏。經(jīng)吸收塔排出的石膏漿液經(jīng)濃縮、脫水,使其含水量小于10%,然后用輸送機送至石膏貯倉堆放,脫硫后的煙氣經(jīng)過除霧器除去霧滴,再經(jīng)過換熱器加熱升溫后,由煙囪排入大氣。
該技術(shù)的反應(yīng)機理為:
吸收反應(yīng):
SO2(g)→SO2(l);
SO2(l)+H2O→H2SO3→H++HSO3-→2H++SO32-
溶解反應(yīng):
CaCO3(s)+H+ → Ca2++HCO3-
中和反應(yīng):
HCO3-+H+ → H2O+CO2(g)
氧化反應(yīng):
HSO3-+1/2O2→H++SO42-;SO32-+1/2O2→SO42-
結(jié)晶反應(yīng):
Ca2++SO42-+2H2O→CaSO4·2H2O(s)
石灰石- 石膏法煙氣脫硫由于初期投資較大,在陶瓷行業(yè)應(yīng)用較少,近些年由于鈣鈉雙減法在陶瓷行業(yè)的弊端,一些企業(yè)開始選擇采用石灰石- 石膏法煙氣脫硫技術(shù)。根據(jù)相關(guān)使用企業(yè)的實際使用效果來看,石灰石- 石膏法完全能夠滿足陶瓷行業(yè)目前的排放標準,并且并無發(fā)現(xiàn)其他和陶瓷煙氣特性不適的問題。但濕法脫硫具有自身排煙濕度大,白霧明顯,在日益嚴格的環(huán)保政策下,煙氣脫白成為目前濕法脫硫必須解決的工藝部分。
3 半干法煙氣脫硫
半干法脫硫技術(shù)是把石灰漿液直接噴入煙氣,或把石灰粉和煙塵增濕混合后噴入煙道,生成亞硫酸鈣、硫酸鈣干粉和煙塵的混合物。采用在濕狀態(tài)下脫硫,是因為干燥條件下堿性吸收劑幾乎不與SO2 發(fā)生反應(yīng),必須有水的存在脫硫反應(yīng)才能進行[8]。而干狀態(tài)下處理脫硫產(chǎn)物主要是在酸堿反應(yīng)進行的同時利用煙氣自身的熱量蒸發(fā)吸收液的水分,使最終產(chǎn)物呈現(xiàn)為“ 干態(tài)”。半干法煙氣脫硫的過程是一個包括了傳質(zhì)、傳熱以及化學反應(yīng)的綜合過程,主要由以下幾步組成:
1)SO2 由氣相向吸收劑顆粒表面的擴散;
2)SO2 在吸收劑顆粒表面的吸附、溶解及離解反應(yīng);
SO2(g)→ SO2(l)
SO2(l)+H2O → H2SO3
H2SO3 → HSO3-+H+ → SO32-+2H+
3)堿性吸收劑顆粒在液相中溶解:
Ca(OH)2 → Ca2++2OH-
4)酸堿反應(yīng)中以固定和脫除硫離子:
Ca2++SO32-+1/2H2O → CaSO31/2H2O
5)脫硫產(chǎn)物水分蒸發(fā),最終以“干態(tài)”形式排出。
一般說來脫硫反應(yīng)總的化學表達式可表示為:
SO2+Ca(OH)2 → CaSO3·1/2H2O+1/2H2O
產(chǎn)物CaSO3·1/2H2O 又有可能被水汽中的O 氧化,生成CaSO4·2H2O 反應(yīng)式為:
CaSO3·1/2H2O+1/2O2+3/2H2O → CaSO4·2H2O
半干法脫硫由于其脫硫效率較低,鈣硫比高,副產(chǎn)物不能商品化,且需增加除塵負荷等原因,其在陶瓷行業(yè)應(yīng)用較少。目前由于陶瓷行業(yè)傳統(tǒng)的脫硫技術(shù)存在的問題,半干法脫硫技術(shù)的優(yōu)勢體現(xiàn)出來,如其具有工藝流程簡單,占地面積小,投資和運行費用較低且無白煙和廢水產(chǎn)生,陶瓷企業(yè)開始嘗試采用半干法脫硫技術(shù)。從目前存在的少數(shù)企業(yè)的運行情況看,由于陶瓷行業(yè)SO2 初始排放值較低,半干法脫硫完全能夠滿足陶瓷行業(yè)的排放要求,且無廢水和白煙產(chǎn)生,完全契合目前的環(huán)保政策。因此,半干法脫硫技術(shù)很有可能成為下一步陶瓷行業(yè)脫硫的主流技術(shù)。
4 結(jié)語
目前應(yīng)用于陶瓷企業(yè)的脫硫技術(shù)各有優(yōu)缺點,隨著時代的發(fā)展和科學技術(shù)的不斷進步,新的優(yōu)化的脫硫技術(shù)仍會產(chǎn)生。陶瓷企業(yè)應(yīng)根據(jù)自身實際,遵循優(yōu)質(zhì)、高效、經(jīng)濟的原則合理地選擇脫硫方案,確保二氧化硫的排放標準控制在國家標準以下,為節(jié)能減排、保護環(huán)境盡到應(yīng)有的責任。
山東新澤儀器有限公司提供的CEMS-8000型煙氣排放連續(xù)監(jiān)測系統(tǒng)采用的紫外差分吸收光譜技術(shù)+抽取冷凝法,抽取式熱濕法CEMS能夠測量SO2、NOx、O2、溫度、壓力、流速、粉塵、濕度等多項參數(shù),并將所有的監(jiān)測參數(shù)傳輸至用戶DCS系統(tǒng),通過數(shù)采儀與環(huán)保部門的數(shù)據(jù)系統(tǒng)通訊。lm
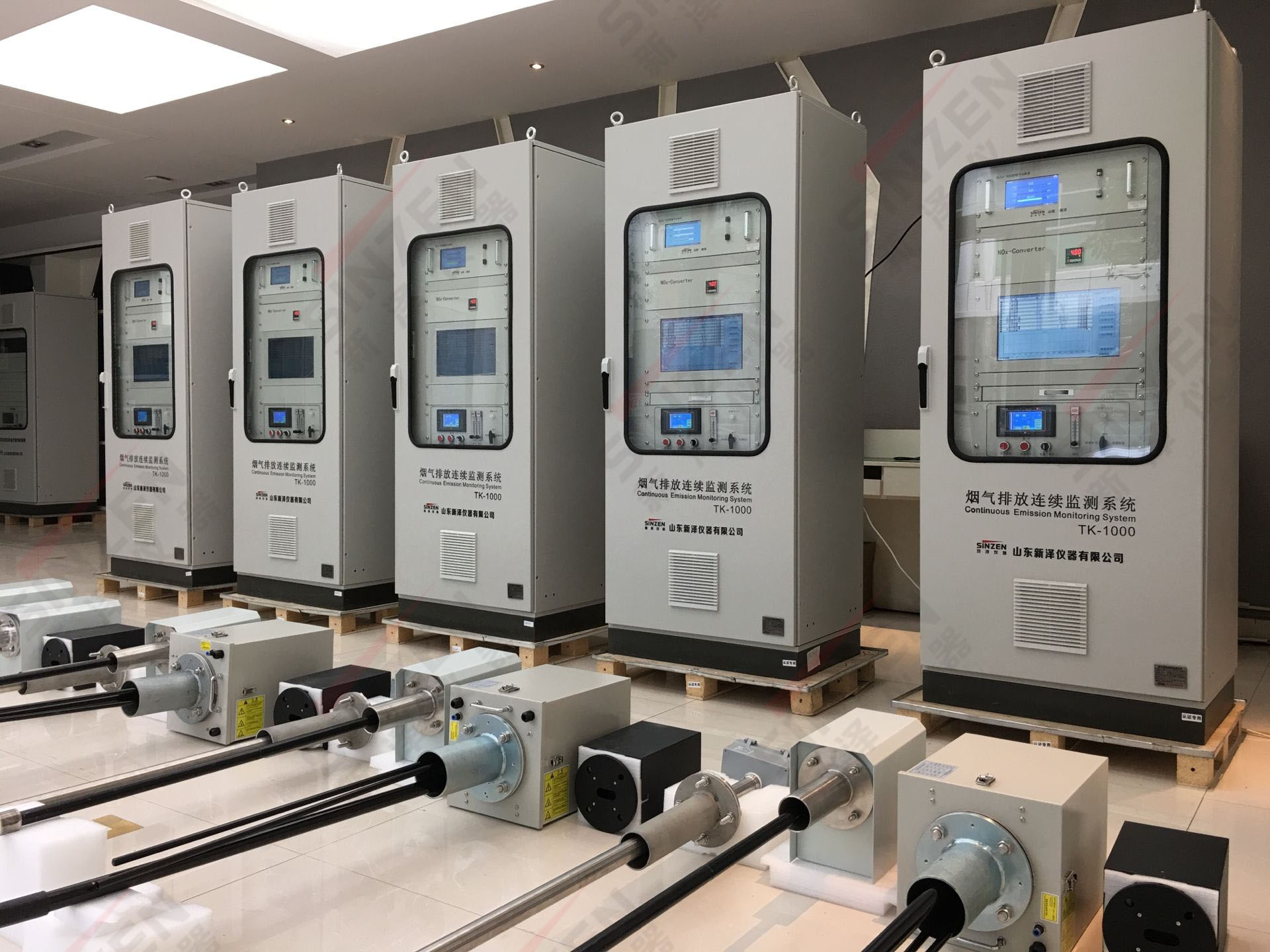